偶联剂改性重钙填充ABS的性能研究
邹检生1 李永安1 彭鹤松1 宋世坤1
(1.江西广源化工有限责任公司,江西吉安,331500)
摘要:采用钛酸酯偶联剂GR-201对超细碳酸钙(GY-616)进行表面改性,改性后的碳酸钙与丙烯腈-丁二烯-苯乙烯共聚物(ABS)制备出ABS/CaCO3复合材料,研究了偶联剂添加量和改性时间对CaCO3吸油值和接触角的影响,测试了复合材料的力学性能和MFR(熔融指数),并用SEM观测了CaCO3粒子在ABS中的分散性。结果表明:经偶联剂处理后,CaCO3吸油值降低,接触角增加;ABS/CaCO3复合材料力学性能提高,加工流动性增加;CaCO3粒子在ABS中的分散性提高。偶联剂添加量为1.5%,改性时间30min,改性效果最佳,复合材料力学性能最佳,加工流动性最好;CaCO3粒子在ABS中的分散性最好。(1.江西广源化工有限责任公司,江西吉安,331500)
关键词:偶联剂,重钙,ABS,力学性能,分散性
0 引言
ABS树脂具有诸多优异特点,广泛应用于机械、汽车、家电等领域。但由于其实际应用的要求不同,需要对ABS树脂进行各种改性,使其达到实际使用要求【1-2】。无机非金属填料进行表面改性处理后,应用于ABS树脂中不仅可降低成本,还能实现性能的提升【3-5】。
由于CaCO3价格低廉,白度好,化学性质稳定,常用于ABS的填充改性。国内大部分学者采用纳米CaCO3填充改性ABS树脂,获得了优异的性能【6-7】。但少见采用重质CaCO3填充ABS的研究,本实验采用超细重质CaCO3填充改性ABS,并对CaCO3粉体改性工艺进行了探讨,详细分析了制备的ABS/CaCO3复合材料的拉伸强度、弯曲强度、冲击强度和MFR的变化,并采用SEM观测了ABS/CaCO3复合材料的冲击断裂面形貌。
1. 实验部分
1.1 原材料
ABS,PA-757,奇美宝业股份有限公司;超细CaCO3,GY-616,D50 3.35μm,D97 5.94μm,江西广源化工有限责任公司;偶联剂,异丙基三(二辛基焦磷酸酰氧基)钛酸酯,牌号:GR-201,市售。
1.2 仪器设备
接触角测定仪:HARKE-SPCAXZ,北京哈科试验仪器厂;双螺杆挤出机组:SHJ-36型,L/D=50,D=35.5mm,南京杰恩特机电有限公司;注塑机:ZX-80型,震雄集团公司;万能力学性能实验机:CMT6104型,美斯特工业系统(中国)有限公司;冲击试验机:ZBC1400-B型,美斯特工业系统(中国)有限公司;MFR仪:ZRZ1452型,美斯特工业系统(中国)有限公司;高速混合机:GRH-100D,阜新鑫克机械制造有限公司;场发射扫描电子显微镜(SEM):SU8010型,日立(中国)有限公司。
1.3 试样制备
1.3.1改性粉体的制备
称取50KgCaCO3加入到高速混合机中搅拌10min去除水分,温度120-130℃,搅拌速度250r/min;去除水分后从改性剂加料口采用塑料滴管滴加偶联剂GR-201,偶联剂的添加量为CaCO3质量的1%-2%;完全滴加完偶联剂后再搅拌一定时间,低速搅拌冷却后出料。对改性后的粉体进行吸油值和润湿接触角的测定。
1.3.2ABS/CaCO3复合材料的制备
按ABS:CaCO3质量份数10:1称取一定质量的原料添加到高速混合机中,搅拌10min,冷却出料;再将混合好的原料加入到双螺杆挤出机中挤出造粒,加工温度设为180-200℃,挤出后的粒子经烘干后进行熔体流动速率测试,另将部分粒子烘干后注塑成标准样条进行力学性能测试。
1.4 性能测试
吸油值测试:按GB/T19281规定方法测试,整个过程要求在5min内完成;润湿接触角测试:取改性后CaCO3压片,采用接触角测定仪测试其接触角,润湿介质为水;拉伸性能测试:按GB/T1040-2006测试;弯曲性能测试:按GB/T9341-2008测试;简支梁缺口冲击性能测试:按GB/T1043.1-2008测试,采用2 J的冲锤,跨度 40 mm;MFR测试:按GB/T3682-2000测试,温度为230℃,压力为5kg;断裂面形貌:样条经液氮淬断后喷金,采用SEM观察断面形貌并拍照。
2.结果与讨论
2.1 偶联剂添加量对吸油值和接触角的影响
吸油值是评价重质CaCO3改性效果的一个重要指标,吸油值越低,表面改性效果越好【8-9】。接触角代表着液体对粉体的润湿性,接触角越大,改性效果越好【10-11】。控制改性时间30min,分别添加1%、1.5%、2%偶联剂,其吸油值和接触角的结果如图1所示。
从图1的结果可以看出,采用偶联剂GR-201对GY-616进行表面改性后,随着偶联剂用量的增加,吸油值逐渐降低;当偶联剂的添加量达到1.5%时,吸油值达到最小值,继续增加改性剂的用量,吸油值并未继续降低。随着偶联剂用量的增加,接触角先快速上升后略有下降,当偶联剂添加量为1.5%时,改性后碳酸钙的接触角达到最大值。与未改性的GY-616相比,采用1.5%偶联剂改性后,粉体的吸油值从26mL/100g下降到18mL/100g,接触角从0°增加到121°,说明偶联剂对CaCO3表面进行了良好包覆,增强了CaCO3粒子的疏水性。由此可见,采用GR-201改性GY-616,偶联剂添加量为1.5%时,改性效果最佳。原因是钛酸酯偶联剂GR201通过化学键偶联在碳酸钙表面,形成了包覆层;随着GR201用量的增加,形成的包覆层对碳酸钙颗粒的包覆完善程度就越高,因此,碳酸钙的吸油量下降,表面接触角增加;当偶联剂的添加量为1.5%时,颗粒表面的包覆达到饱和状态,继续添加偶联剂,对颗粒的吸油量不再产生影响;然而,继续增加偶联剂,多余的偶联剂中的非极性基团与颗粒表面的非极性基团相互缠绕,极性基团则向外排列,从而导致接触角下降。
2.2 改性时间对吸油值和接触角的影响
控制偶联剂添加量为1.5%,改性时间分别为10min、20min、30min、40min、50min,其吸油值和接触角的结果如图2所示。
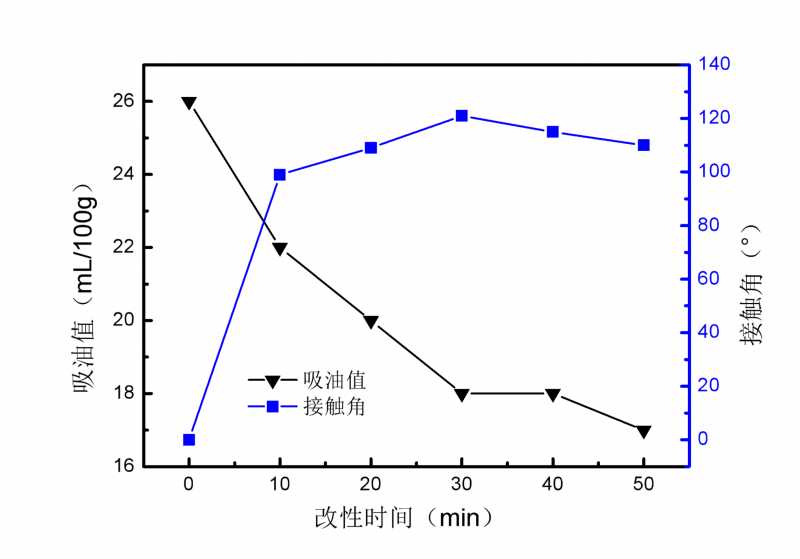
图2 改性时间对吸油值和接触角的影响
从图2的结果可以看出,随着改性时间的增加,采用偶联剂GR-201处理后的GY-616吸油值逐渐降低;当改性时间达到30min时,吸油值变化趋于平缓,虽然继续增加时间吸油值略有下降。随着改性时间的增加,接触角先上升后下降,在改性时间为30min时接触角最大。综合考虑生产成本,改性时间为30min时,GR-201改性GY-616的效果最佳。原因是随着混合时间的增加,偶联剂与颗粒表面反应更为完全,包覆更为均匀,但是时间太长,机械力会导致偶联剂分子破坏,反而损害包覆完整性,导致接触角下降。
2.3偶联剂添加量对复合材料性能的影响
控制改性时间30min和添加量为10份的情况下,分别选取添加1%、1.5%、2%偶联剂的改性GY-616填充改性ABS,ABS/CaCO3复合材料的力学性能和流动性能如图3所示。
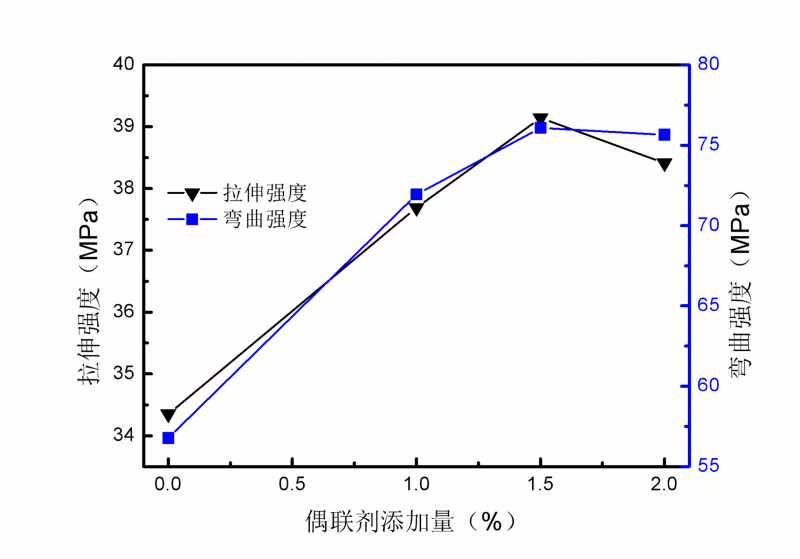
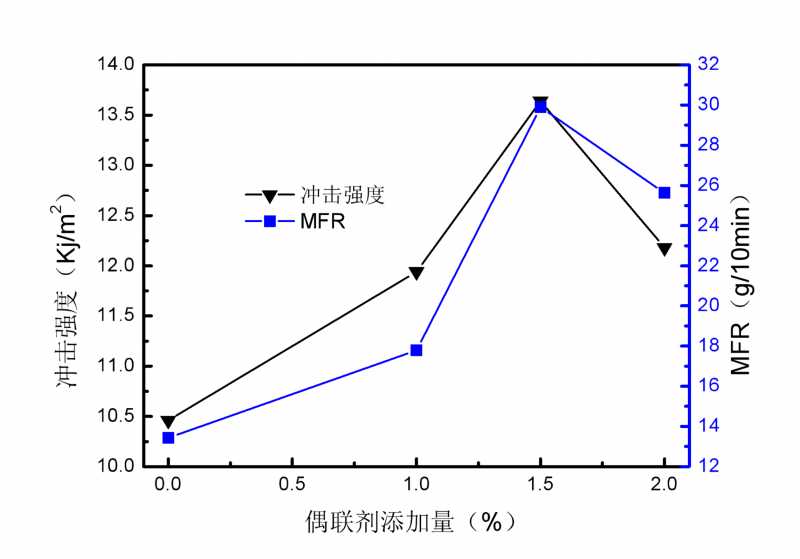
图3(a)是偶联剂添加量对ABS/CaCO3复合材料的拉伸强度和弯曲强度的影响,图3(b)是偶联剂添加量对ABS/CaCO3复合材料的冲击强度和MFR的影响。从图3(a)可以看出,随着偶联剂添加量的增加,复合材料的拉伸强度和弯曲强度先上升后下降,在偶联剂用量为1.5%时,拉伸强度和弯曲强度达到最大;同时与未改性CaCO3制备的复合材料相比,经过偶联剂处理后,其拉伸强度和弯曲强度得到了提升。从图3(b)可以看出,随着偶联剂添加量的增加,复合材料的冲击强度和MFR先上升后下降,在偶联剂用量为1.5%时,冲击强度和MFR达到最大;同时与未改性CaCO3制备的复合材料相比,经过偶联剂处理后,其冲击强度和MFR得到了提升。由此可见,偶联剂添加为1.5%时,颗粒表面形成了较为完善的包覆层,该包覆层与颗粒和ABS都有较好的粘结作用,从而增强颗粒与ABS之间的粘结,提高复合材料的力学性能,因此,此时ABS/CaCO3复合材料的力学性能最佳,加工流动性最好,这与吸油量和表面接触角的分析结果一致。
2.4改性时间对复合材料性能的影响
选取偶联剂添加量为1.5%和添加量为10份的情况下,改性时间分别为10min、20min、30min、40min、50min,制备的ABS/CaCO3复合材料的力学性能和流动性能如图4所示。
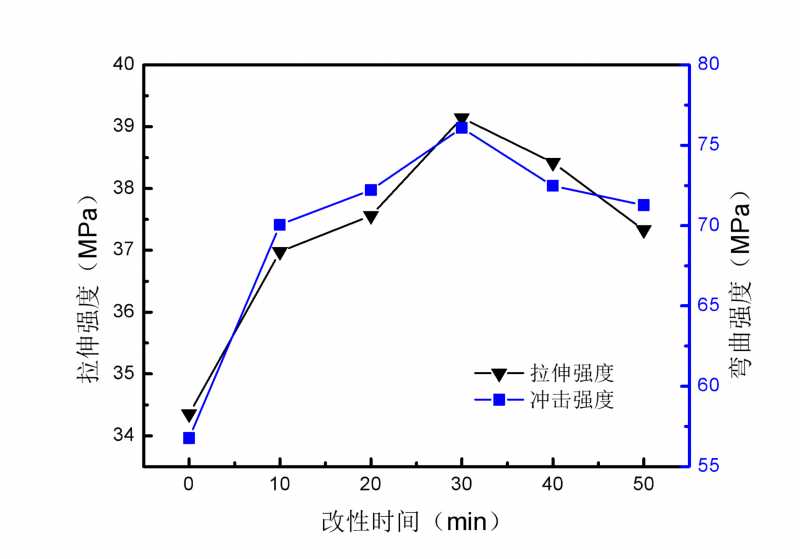
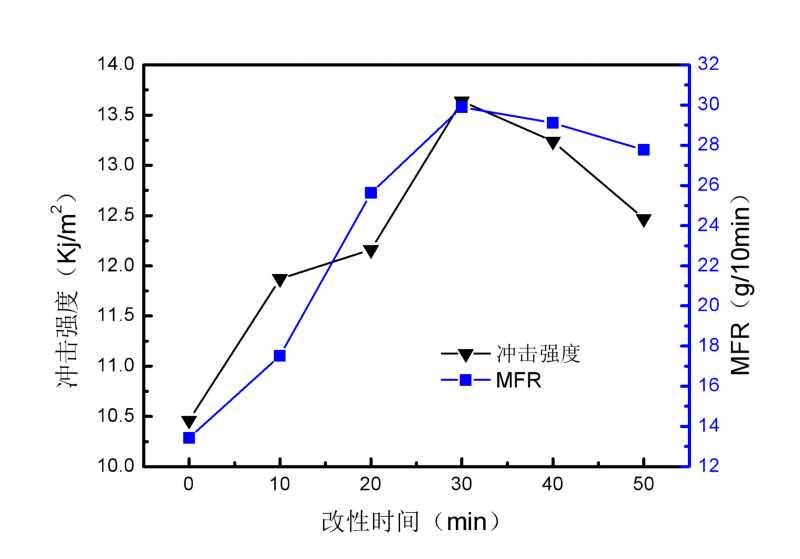
图4改性时间对复合材料性能的影响
图4(a)是改性时间对ABS/CaCO3复合材料的拉伸强度和弯曲强度的影响,图3(b)是改性时间对ABS/CaCO3复合材料的冲击强度和MFR的影响。从图3(a)可以看出,随着改性时间的增加,复合材料的拉伸强度和弯曲强度呈现先上升后下降的变化趋势,当改性时间为30min时,拉伸强度和弯曲强度达到最大;同时与未改性CaCO3制备的复合材料相比,经过偶联剂处理后,其拉伸强度和弯曲强度得到了提升。从图3(b)可以看出,随着改性时间的增加,复合材料的冲击强度和MFR先上升后下降,当改性时间为30min时,冲击强度和MFR达到最大;同时与未改性CaCO3制备的复合材料相比,经过偶联剂处理后,其冲击强度和MFR得到了提升。由此可见,随着混合时间的增加,偶联剂与颗粒表面反应更为完全,包覆更为均匀,与基材的粘结作用也更强,但是时间太长,机械力会导致偶联剂分子破坏,从而导致改性后的颗粒与基材之间的粘结作用变弱,复合材料的力学性能下降,因此,改性时间为30min时,ABS/CaCO3复合材料的力学性能最佳,加工流动性最好。2.5复合材料断裂面形貌分析
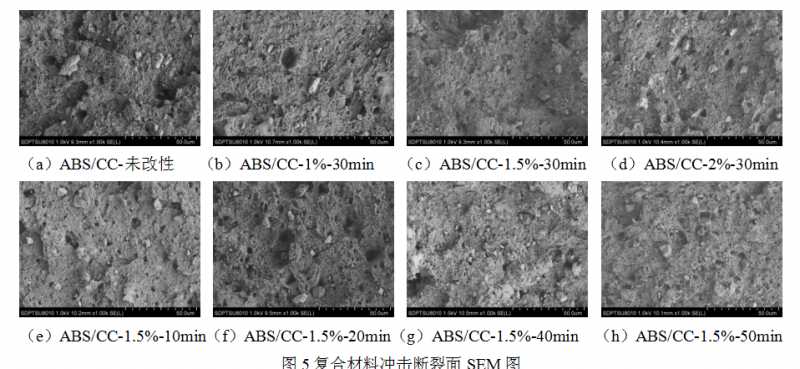
图5复合材料冲击断裂面SEM图
为了探讨改性CaCO3对ABS的增强作用,研究不同改性工艺CaCO3在ABS中的分散性,采用SEM对冲击样条的断裂面进行观测,结果如图5所示,放大倍数为1000倍。从图5(a)可以看出,采用未改性CaCO3与ABS制备复合材料,冲击断裂面上存在着较多大的颗粒,并且颗粒与孔洞之间的粘结不强,说明未改性CaCO3粒子存在着一定团聚,分散性欠佳。从图5(b)(c)(d)可以看出,在改性时间为30min,偶联剂添加量分别为1%、1.5%、2%时,(b)、(c)和(d)图中的孔洞和颗粒,但相对于(a)图,其颗粒要小,分散性和粘结性都要好;其中,(c)图粒子分布均匀连续,颗粒较小,分散性最佳。从图5(e)(f)(c)(g)(h)可以看出,偶联剂添加量为1.5%,改性时间分别为10min、20min、30min、40min、50min时,图(e)(f)(g)(h)都存在着一定的孔洞和颗粒,但相对于(a)图,其颗粒要小,分散性要好;(c)图粒子分布均匀连续,颗粒较小,分散性最佳。由此可见,经过偶联剂处理后,CaCO3粒子在ABS中的分散性有所改善;在偶联剂添加为1.5%,改性时间30min时,CaCO3粒子在ABS中的分散性最好,这与之前的分析结果一致。
3 结论
采用钛酸酯偶联剂GR-201改性重钙(GY-616)填充ABS树脂,结果表明:
1)经过偶联剂处理后,CaCO3吸油值降低,接触角增加。偶联剂添加量为1.5%,改性时间30min,改性效果最佳。
2)经过偶联剂处理后,ABS/CaCO3复合材料力学性能提高,加工流动性增加。偶联剂添加量为1.5%,改性时间30min,ABS/CaCO3复合材料的力学性能最佳,加工流动性最好。
3)经过偶联剂处理后,CaCO3粒子在ABS中的分散性有所提高;在偶联剂添加量为1.5%,改性时间30min时,CaCO3粒子在ABS中的分散性最好。
4 参考文献
[1] 刘媛,王卫卫,周琦等. 无机填料改性ABS树脂的研究[J]. 塑料助剂, 2008, 68(2): 34-38.
[2] 彭鹤松,曾伟,宋建强等. 永丰超白大方解石粉在ABS中的应用[J]. 工程塑料应用, 2016,44(8): 115-119.
[3] 梁基照. 超微细CaCO3填充ABS复合材料的力学性能[J]. 现代塑料加工应用, 2005, 17(1): 16-18.
[4] 张凌燕, 赖伟强, 唐华伟等. 硅灰石改性及填充工程塑料ABS的研究[J]. 非金属矿, 2007, 30(3): 23-25.
[5] 张凌燕, 唐华伟,赖伟强. 白云母改性与填充ABS工程塑料的试验研究[J]. 塑料, 2007, 36(4): 5-7.
[6] 宋继瑞,沈志刚,陈建峰等. ABS/改性纳米CaCO3复合材料的微观结构和力学性能[J]. 高分子材料科学与工程, 2004, 20(3): 126-128.
[7] 孙树林, 张会轩, 张皓瑜等. 纳米CaCO3/ABS复合材料的制备[J]. 吉林工学院学报, 2001, 22(3): 32-34.
[8] 汤泉,陈瑞琼,卢玉昌等. 松香酸烷醇酰胺表面改性重质碳酸钙的研究[J]. 化学工程师, 2012, 3:11-13.
[9] 周学永, 尹业平, 钟万维. 硬脂酸改性碳酸钙的效果表征与改性机理初探[J]. 广东化工, 2006,33(2): 24-26.
[10] 李丽匣, 韩跃新, 陶世杰. 碳酸钙晶须表面改性研究[J]. 化工矿物与加工, 2008, 5: 4-8.
[11] 邹海魁, 陈建峰, 刘润静等. 纳米CaCO3的制备、表面改性及表征[J]. 中国粉体技术, 2001, 7(5): 15-18.